课题解决案例
我们希望开发出能够满足新型电动汽车需求且具有未来感的时尚内饰…
一次性解决设计性、表面硬度、环保等课题的新薄膜材料
汽车内饰零部件厂商G公司 设计开发部
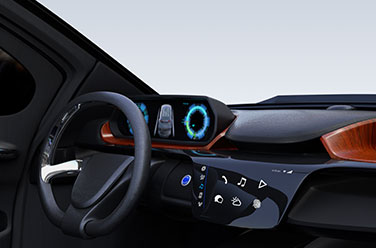
G公司收到了汽车厂商通过汽车零部件厂商发出的新型电动汽车内饰用途的开发委托。开发出具有未来感的外观设计相匹配的智能化内饰是汽车厂商的设计师提出的强烈要求。另一方面,根据环保采购方针,资材部提出了降低零部件生产工序中的环境负担的要求。设计开发部对如何同时满足上述要求而倍感困惑。
课题
想开发出摒除实体按钮的发光透显的“透光显示+静电开关”…
G公司负责开发的零部件是仪表板中央的一个重要组成,用于操作空调和其他控制按钮均集中于此。设计师提出的要求是,这些按钮应采用时尚的形式,而不是传统的物理实体按钮或者拨动开关。
在收集最新信息的过程中,设计开发部的主管人员判断“透光显示+静电开关”符合客户的要求。G公司拥有印刷薄膜的模内成型性零部件量产经验,因此,如果此次印刷部分使用透光印刷,并采用静电开关设计,应该可以满足客户的要求。但是,在试制阶段,热成型薄膜却出现了问题。
在透光显示中,透光部分(字符和符号)对位置精度的要求极高,因此,在进行模内成型前的薄膜热成型时,需要使用成型性能良好的薄膜。但是,表面硬度高的薄膜会出现热成型性能不佳的情况,这就是实现本次创意的最大难点。此外,从资材部提出的“环保采购方针”的角度来说,零部件的选择也是一大难题。
开发团队成员亟需找到一种不同于传统方式的生产工艺。
课题关键点
- 为了满足设计师的要求,计划采用“透光显示+静电开关”设计,但发现所使用的热成型薄膜存在问题
- 拥有实际量产经验的使用热成型薄膜的工艺,无法兼顾表面硬度和热成型性能
- 从资材部提出的“环保采购方针”的角度来说,零部件的选择也是一大难题
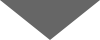